High performance, reactive, predictive: these are the hallmarks of the
complete 4.0 cap preform manufacturing line, which SACMI will preview for the Chinese market on the
WeChat platform.
With a share of over 70% on the compression cap manufacturing market, SACMI is the #1 technology provider in China and leads the way in
digitally revolutionizing rigid packaging lines.
This initiative aims to offer an overview of all the latest products and services: hence the development of a
dedicated landing page on the platform, where customers can obtain in-depth info on everything that would have been presented at the recently postponed
Chinaplas 2022 fair.
Re-action
The first crucial tools are the
on-machine sensors and controls and the advanced monitoring-control functions that minimize waste and predict any deviations from process parameters. On CCM cap-making compression presses, this has led - following months of hard work alongside customers worldwide - to the development of an unprecedented
optional ‘Smart Pack’. Available across the entire range, the latter merges all the latest digital controls in a single package.
These include dose insertion and positioning control, a feature that makes adjustments faster and easier whenever material or size changeovers are required. Key advantages include being able to predict malfunctions caused by wear or incorrect settings.
Smart pack provides enormous added value by simplifying workers’ tasks, increasing system availability and lengthening component lifespans. It also includes a predictive tool that optimizes maintenance (by monitoring the condition of the hydraulic oil, temperatures and any condensation on the molds). Above all, with Smart Pack the press can perform independent, real-time recognition of any resins that fail to match the product recipe, thus preventing any waste of materials, time or man-machine resources.
Feedback on the process
With over 670 cap machines and numerous preform presses installed by the industry’s leading players, SACMI is the Chinese rigid packaging industry’s leading partner. SACMI aims to take the digital revolution to its customers in this sector by implementing advanced monitoring-control functions and solutions that allow them to correct errors and optimize production.
To start with, there’s the option of integrating advanced
Computer Vision Software solutions into its CCM and IPS (
injection preform system) range. Such systems are characterized by next-gen hardware and data capture devices and intelligent algorithms; as of today, they constitute not just a tool for detecting defects on products but, above all, one that lets manufacturers
gather vital information for correcting and optimizing the process. A few examples: the new
IPS 300 preform press recently presented by SACMI, a unique solution as it allows
direct integration of the vision system (PVS) inside the machine. On
cap lines, instead, users can set thresholds for defects or parameter deviation which the system then uses to predict the relative consequences before any actual problems can arise.
Prevention & prediction
The last step in the digital revolution involves interconnecting machines and production departments, thus extending the concept of performance to
monitoring-tracking of individual batches during production, interfacing with
order management and
maintenance planning to minimize impact on line availability.
Called HERE, this platform has been specifically designed for the industrial processes in which SACMI is the world leader, that is, the machines and plants used to manufacture ceramics and packaging.
With HERE, manufacturers can keep track of production plant status, supplies, any problems and their causes: all via a single interface, which can be accessed anywhere, from any device connected to the company network.
SACMI’s digital revolution will allow its rigid packaging customers to boost plant profitability through improved planning of man-machine resources. That’s why, with SACMI,
production is moving in-cloud via the innovative ‘Smart Care’ proposal.
Thanks to the new IoT service that generates, gathers and manages machine-plant data, customers can keep tabs on the medium-long term ‘health’ of the entire machine, taking process control - and the relative economic returns - to unprecedented heights.
What’s more, customers can interface their machines directly with the SACMI server to benefit from advanced plant ‘health checks’ and ‘
proactive problem solving’ services. Again, there’s an immediate
economic advantage that stems from, for example, being able to predict maintenance tasks on the basis of actual operating data.
Visit the dedicated landing page on the WeChat digital platform.
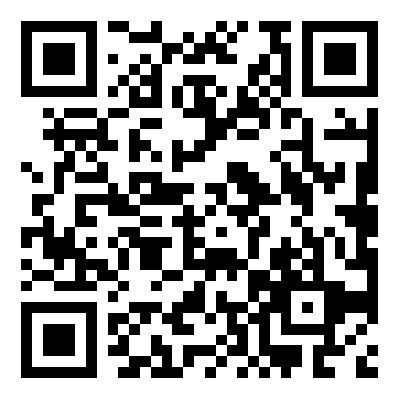
Rigid packaging digital r-evolution by SACMI. Always at your side.